EFFECTIVE SUPPORT FOR SCHEDULING - INTELLIGENT SOFTWARE EXPANDS PLANNING HORIZON
Schmitt+Sohn Elevators produces and modernizes elevator systems. For optimal inventory management, the production and spare parts supply requirements are coordinated with the ADD*ONE solution suite for the Inventory Optimization application area. Thanks to well-founded forecasts, the company quickly noticed an optimization of its work and expects to reduce its inventory by 25%.
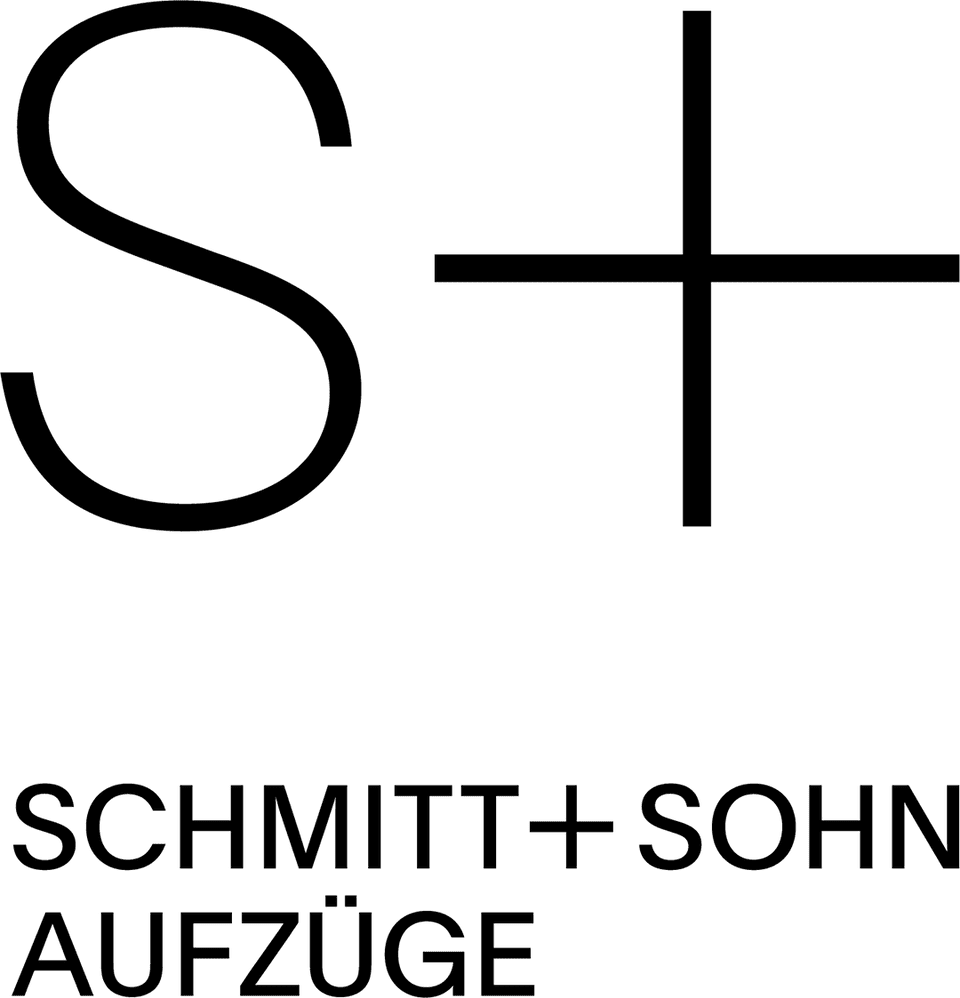
The confusing lists that our system output made it difficult to evaluate the figures in a meaningful way. The schedulers had to rely heavily on their gut feeling regarding the accuracy of this order information. It was unclear whether the displayed items would even be needed in the future, and if so, in what quantity. In order not to have too little in stock, we tended to order too much. Our stock value increased from year to year and tied up too much capital.
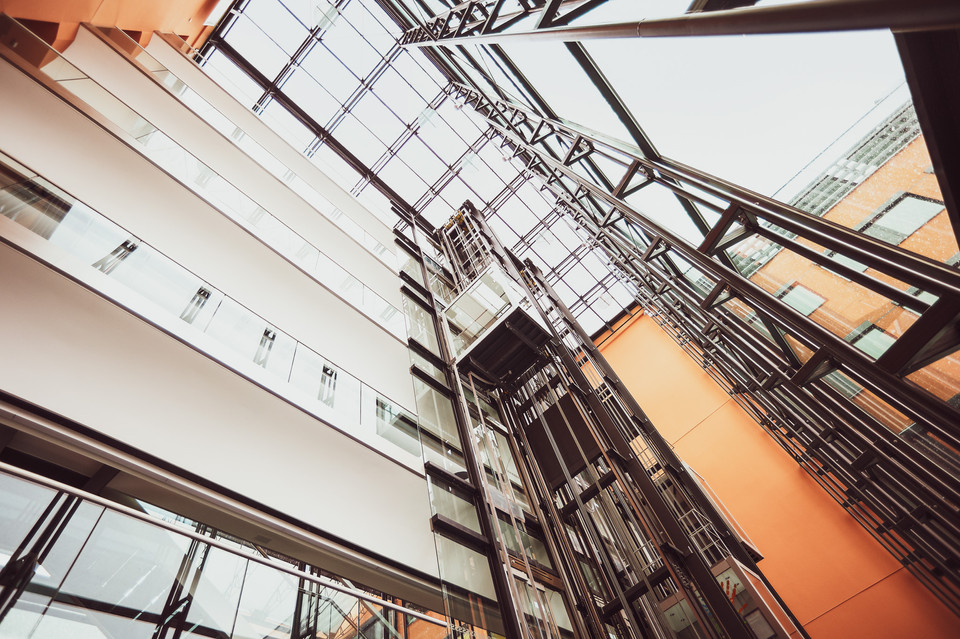
Due to the production of elevator systems according to individual customer requirements, a correspondingly large number of variants, and a short lead time of only four to six weeks, long-term advance planning of specific requirements for production and spare parts supply was hardly possible. Along with the constant growth of the company, Schmitt+Sohn Aufzüge, therefore, repeatedly ran the risk of having to stop production because the required parts were not available in time.
“The production department was sometimes only able to notify us of missing items at the moment when they were already needed. That was fatal, of course,” recalls Stefan Rohde, Process Owner of Purchasing/Materials Management at Schmitt+Sohn.
“In addition, our suppliers ideally want to know a year in advance which materials we will purchase. Among other things, the changing prices for raw materials such as stainless steel or plastic are responsible for this. Here, too, we have had to rely far too often on our gut feeling and fall back on static past values for our material planning.”
The need to reduce the inventory value and at the same time to have the right materials at the right time made it clear: Without an IT-based solution, it is no longer possible. As a supplement to the existing ERP system, the ADD*ONE solution suite now handles planning and creates order proposals. Schmitt+Sohn reports about the introduction of the solution suite for inventory optimization: “The acceptance of the software on the part of the employees is high because they quickly recognized the advantages. We do noticeably less troubleshooting on the shop floor because the system alerts us to missing stock in good time. This gives us the certainty that production will not come to a standstill.”
CHALLENGES
- Enormous increase in stock value due to increasingly individual installations and a lifespan of the elevators of at least ten years
- Risk of production downtime due to missing materials
- No sufficient support in order optimization and demand forecasting by the ERP system
RESULTS
- Longer-term planning horizon and significantly less troubleshooting in production
- Strong simplification in the scheduling processes and thus more time for strategic tasks
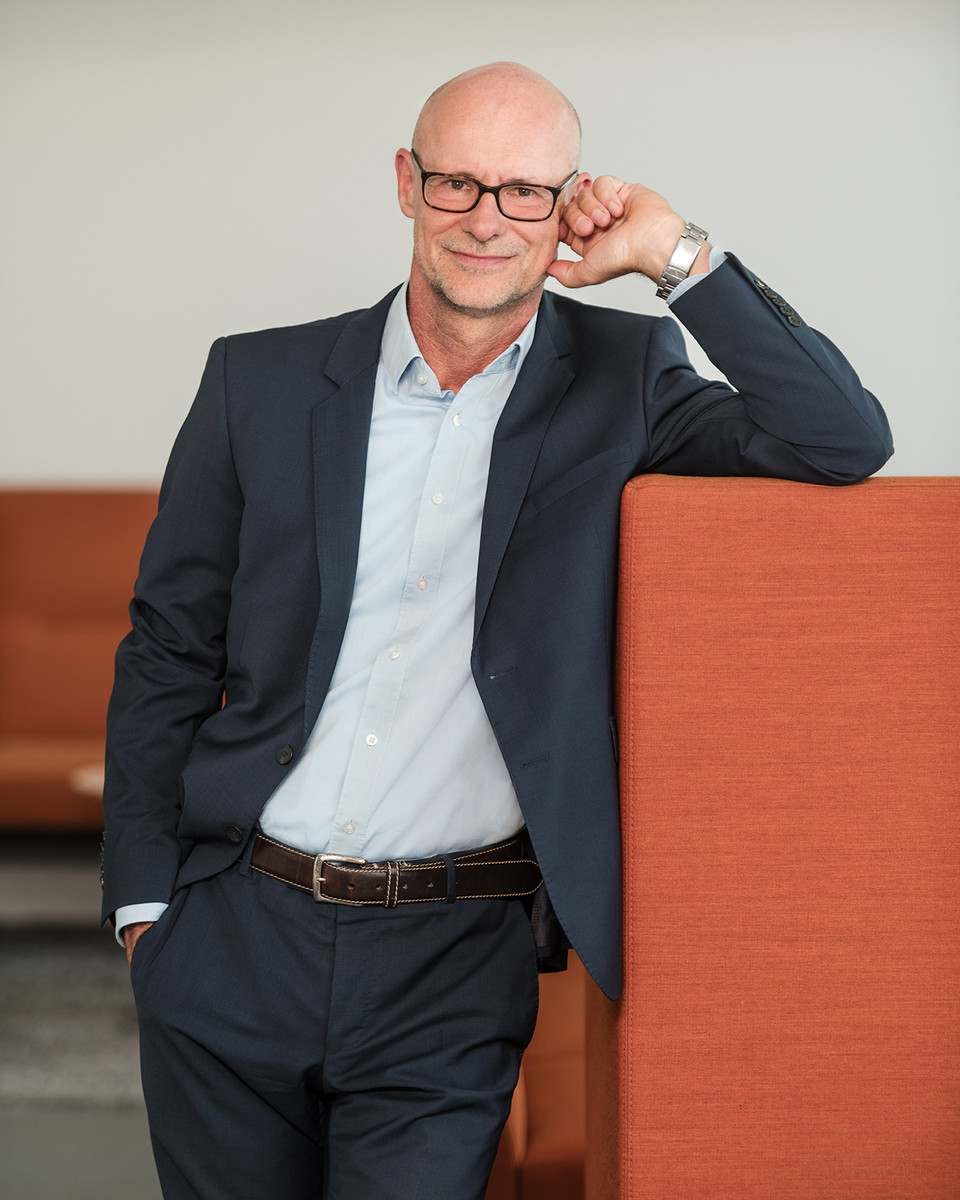
Andreas Schäfer
Expert for Supply Chain Optimization
Andreas Schäfer has been working for INFORM GmbH in the Inventory & Supply Chain division since 1999. In his role as sales manager, he supports interested parties from the supply chain sector in the decision-making process for selecting the optimal planning software.