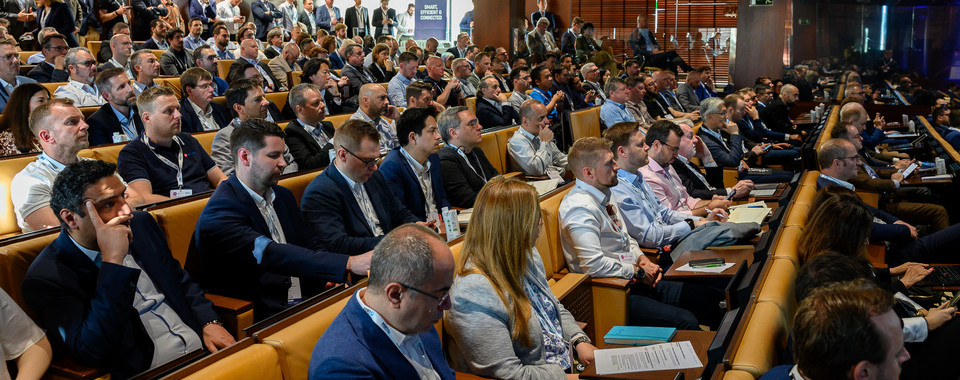
Apr 16, 2025 // Kira Biernat
Navigating Change in the Container Terminal Industry
Trends and Truths from CTAC 2025
Oct 1, 2020 Matthias Wurst
Share© vm | gettyimages
The idea of separating delivery and unloading is not new. It has been practiced in postal and parcel centers for years. The method is also increasingly used in the automotive industry in the form of traileryards. After delivery to the factory, the trailer is not unloaded directly but parked in an area that resembles a large parking lot – the traileryard. There, not only semi-trailer and trucks are segregated, but also unloading is separated from truck arrival. This flexibility brings a number of advantages – increased throughput times, higher yard safety, and even sustainability, to name a few. Prerequisites are sufficient space and the willingness to invest.
The truck parks the trailer with the delivery goods in the yard.
The truck picks up a new trailer with finished goods or one that is empty.
A terminal tractor, aka “yard dog,” lifts the trailer and tows it to the correct loading point at the plant.
Empty trailers are placed in the traileryard by the terminal tractor for removal.
A trailer yard separates delivery traffic and in-plant traffic, which has advantages for both sides. This has very practical effects on the delivery process. For example, there is no need to check the personal protective equipment that the truck driver would need at a loading dock in the facility. Language barriers are eliminated, as it is often difficult to direct the orientation of non-local drivers on the plant premises.
A trailer yard, therefore, also increases safety on the site.
Having fewer external people in the plant also contributes to infection control, which employers currently have to comply with anyway. This is a relevant factor, especially given the often hundreds of trucks that enter the facility every day and whose drivers have had many interregional contacts. Security for sensitive R&D, such as newly developed prototypes, is also easier the fewer visitors a facility has.
Trailer yards are sustainable because CO2 emissions are reduced. Internal tractors are smaller or are already electrically driven ( See this article: UPS tests autonomous-enabled electric shifters to move trailers). Under certain circumstances, a compound for buffer storage can also be avoided, as the trailer yard itself serves as a buffer. This saves loading capacity and storage space.
The most obvious advantage, however, is the reduced waiting time of the inbound trucks to less than one hour on average. This means that drivers and trucks are available to transport traffic again almost immediately. Instead of a turnaround time of two to three hours, the truck can be re-saddled within 30 minutes and perform its intended task, carrying and delivering freight.
The entire subsequent supply chain benefits from this acceleration.
The efficiency of a trailer yard depends on the level of dwell time reduction and the number of inbound trucks per day. If, for example, the throughput time is two hours with regular docking and two hours with trailer yard procedures, throughput time is reduced by 50 percent. The saving of one hour dwell time per trip is therefore 100 hours assuming 100 deliveries per day. Suppose truck drivers work nine hours a day. This corresponds to a calculated saving of around eleven drivers.
This calculation shows that trailer yards increase the capacities of the entire transport logistic system.
The advantages speak for themselves, but a trailer yard cannot be used everywhere because the space requirement is very high. For fully developed industrial areas or facitilities in urban environments, hardly any space will be available without deconstruction. However, it may be possible to convert existing parking spaces if, for example, they are already being used for the trucks to arrive the evening before.
Of course, there are some restrictions on which trailer may be moved by which carrier. Therefore, facilities with fixed carriers are particularly suited to this concept allowing each carrier company to swap its own trailers. It should also be considered that in most cases there will still be a small amount of non-semi-truck-delivery that is unsuited for the trailer yard concept.
Keeping track of the numerous parked trailers still remains a real challenge. What is stored in which trailer? When does which trailer have to go to which loading dock for loading and unloading? Which empty trailers can be taken by which transport company? In order to fully utilize the potential of the trailer yard, an intelligent logistics software is required that skilfully interweaves transport logistics and intralogistics. Trucks should arrive in time slots so the trailer yard can be loaded in a sensible order and without congestion at the gate.
Intelligent Software algorithms can also be used to manage autonomous vehicles at the site. The use of such vehicles is easier to implement on closed plant premises than on public roads. Already, automated guided vehicles (AGVs) are used in warehouses and on manufacturing floors. Autonomous transfer vehicles, such as the Terberg AutoTUG, already exist for the use in the trailer yard. For larger facilities like maritime or multimodal terminals, autonomous towing vehicles are also already being developed. See this article: Volvo Trucks - Introducing Vera, the Future of Autonomous Transport. But, even if in the distant future all transport traffic will be autonomous, the benefits of trailer-hand-over remain.
Without waiting for technical breakthroughs in the industry, new approaches are conceivable with a trailer yard. The driver takes a break (required by law) while the trailer is being exchanged and can use his working time in transport. Perhaps there would be a break area specially set up for this purpose. Driver shortages and rising transport costs affect every production and do not stop at the gate.
Take a look at our Yard Management Solution that features a Trailer Yard Module.
About our Expert