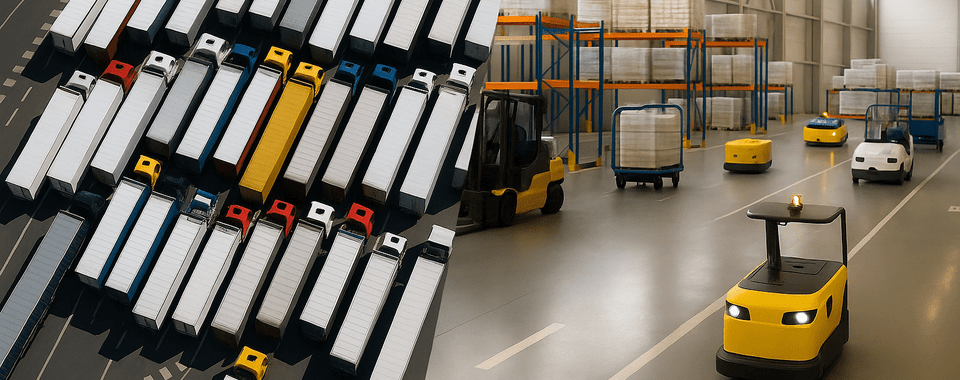
Jun 10, 2025 // Zdravka Ley
Fleet management rethought: How intralogistics is redefining the term
From classic fleet management to a networked and flexible intralogistics management system.
Dec 15, 2021 Ulf König
ShareThere are millions of ways to organize internal transport - but which is the right one?
Getty Images
The digital transformation in intralogistics is strongly characterized by the use of autonomous vehicles. In many cases, however, these autonomous fleets are deployed in clearly defined areas and/or process steps. The fleet of conventional transport vehicles and people therefore often remain separate from autonomous systems. Even when autonomous vehicles are operated together in the same area as conventional transportation systems and people, in so-called hybrid fleets, the control of the systems often (still) remains separate.
This separation hinders the full utilization of the potential of AGVs (automatic guided vehicles) and the further potential through the overall increase in efficiency of intralogistics. By creating boundaries along the means of transport used without a common control level, intelligent control and optimization across the entire value stream are hindered. We will now look at how such an intelligent system can keep track of all internal transports and put all orders in an optimized sequence.
Most industrial companies still rely on forklifts as the most important means of transport for order processing. This is confirmed by INFORM's Trend Report Intralogistics 2021. However, AGVs are already being used in 25 percent of the German industrial companies surveyed. Compared to an intralogistics survey in 2013, this is more than double. At that time, it was only 11.6 percent. Overall, therefore, in-plant logistics is developing positively and the digitization and automation of processes now seem to be on the agenda of many specialists in intralogistics.
However, AGVs are not yet taking over in-plant transport across the board. One of the reasons for this is that not every vehicle is suitable for every type of transport goods. If the goods to be transported vary significantly from the conventional pallet or box, AGV acquisition costs can quickly rise. To this end, the introduction of an AGV requires good organization and planning. Once introduced, systems are usually not as flexible as conventional forklifts. It is often difficult to use AGVs in a cost-effective manner for frequently and rapidly changing processes. This raises the question of whether a hybrid use of AGVs and forklifts is not the better solution for in-plant logistics. But how can human-controlled and self-propelled industrial trucks be controlled together?
For a hybrid fleet to operate, systems are needed that network AGVs and manually controlled forklifts and control all vehicles from a meta-perspective as a so-called control system. VDA 5050 is an interface standardized by the German Association of the Automotive Industry (VDA) and the German Mechanical Engineering Industry Association (VDMA) for communication between automatic guided vehicles (AGVs) and a control system. It creates the basis for networking AGVs from different manufacturers and brings heterogeneous systems into one environment. Why is such an interface necessary? AGVs are usually purchased as a complete package from the AGV supplier. They then contain a partial control system and sensor technology, but the AGVs from different manufacturers, in particular, do not communicate with each other.
The SYNCROTESS transport control system uses optimization algorithms based on artificial intelligence, which can make ad-hoc conclusions from the specific situation as to which transport vehicle should carry out which order next so that the entire order network functions optimally and empty runs are avoided. The system combines all relevant information for dispatching, controlling, and monitoring resources and transport orders while synchronizing the processes. This enables companies to minimize the use of resources while maximizing their transport performance.
The VDA 5050 interface also turns SYNCROTESS into a control system for the entire internal transport logistics. The software communicates with vehicle types of all kinds and can assign each transport order as required so that an overall optimum is achieved. Whether a forklift, an AGV, or a tugger train fulfills the order is decided independently by the software, taking into account all parameters and general conditions. The transport is transmitted to the vehicle, which sends back its status in real time. This creates maximum transparency, which enables a quick response in the event of a malfunction. In addition, more transport orders can be completed in less time, as the system distributes all transports in a route-optimized and time-optimized manner. The conflict between AGVs and manually controlled forklifts is thus eliminated, as the format mismatch has been removed.
Fleet operators can scale their transport performance at any time by adding new conventional or automated transport equipment (regardless of manufacturer and existing systems) to the fleet. The hybrid fleet functions efficiently and points the way to the future of intralogistics.
About our Expert
Ulf König
Head of Business Development Manufacturing Logistics
Ulf König joined INFORM in 2021 and is responsible for strategic business development in the Manufacturing Logistics Division. He works closely with the team and customers to drive joint efforts for sustainable digitalization, improved decision-making and increased efficiency in logistics.