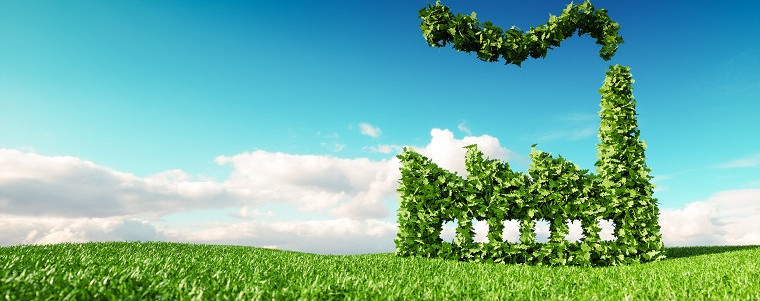
Feb 3, 2021 // Stipo Nad
Green Production Planning - Resource-Efficient and Sustainable Production
Due to high CO2 emissions, many industries are coming under increasing pressure to reduce their emissions. The machine and system engineering sector is also increasingly feeling this demand.