COPPER PRODUCER SIGNIFICANTLY REDUCES REPORTING EFFORT FOR stocktaking THROUGH ADD-ON SOFTWARE
The world’s third-largest copper producer and recycler, Aurubis AG, relies on INVENT XPERT inventory sampling software for its annual stocktaking. Now, only 8% of all items have to be counted manually. The software takes care of the rest. The result can be transferred to the auditor at the push of a button. In this way, Aurubis now completes the stocktaking in a fraction of the time previously required.
Talking to INFORM, we found that with the help of INVENT XPERT, we can solve many of our problems. The system makes the projections transparent for us, and the graphical representations are very clear. The most helpful thing for us is that the software is able to evaluate the result and provide complete reporting for download.
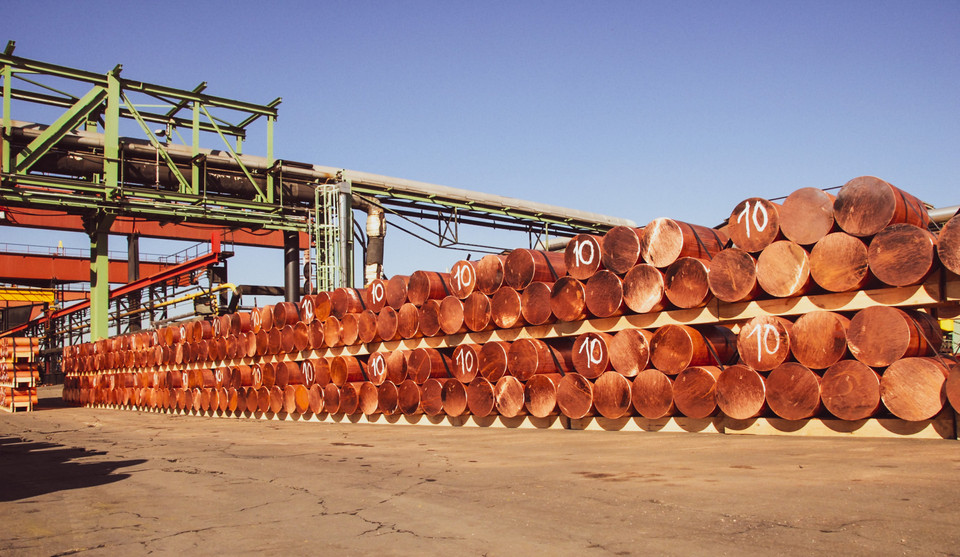
For the copper group, Aurubis, a well-managed warehouse is the be-all and end-all. For example, in order to quickly prevent a costly production standstill with the right repair parts in the event of damage in production. However, the stocktaking previously carried out via an additional application of the existing SAP system generated a disproportionately high reporting and evaluation effort. Moreover, for Aurubis, a careful stocktaking is not only a measure prescribed by law but also a useful addition to inventory management. This is why the copper producer relies on the INVENT XPERT add-on software.
In addition to the intelligent evaluation options, Aurubis was also impressed by the web-based interface, where employees can see how the stocktaking is calculated. For example, they can see how full stocktaking and sampling shifts are formed or where there are outliers in the stocktaking. In the LES-managed warehouse with barcode use, items that have not been confirmed cannot be counted and belong in the recount, which is also displayed in the software.
INVENT XPERT is connected to the warehouse management software as an add-on system via a standardized SAP transaction. At the beginning of the stocktaking, all data is first transferred to INVENT XPERT via an interface from SAP, where it is prepared for the mathematical-statistical procedure. Then, a random sample is drawn. The data then flows back to SAP. The usual stocktaking process in the warehouse management system can now be continued. However, thanks to the random sample, this list now only includes 8% of the total 35,000 parts. The warehouse remains in operation. Only the respective storage bins that are currently being counted are blocked for the duration of the count.
The responsible employees were able to pass on the evaluated result directly to the auditor instead of having to laboriously gather them together as in SAP. In addition, INVENT XPERT makes the detailed evaluations, lists, and protocols available in one place at the push of a button.
CHALLENGES
- High personnel and time expenditure
- Disproportionately high reporting and evaluation effort in the existing SAP system
- Provided data could not be handed over to the auditor without intensive post-processing
RESULTS
- Carrying out the inventory sampling parallel to the day-to-day business without closing the warehouse
- Only 8% of all items can be counted manually
- Reduction of reporting time from 1.5 weeks to two to three hours
- Connection of INVENT XPERT to SAP-R3 interface