Würth brings transparency and precision to yard logistics with INFORM
The Würth Group is the global market leader in the development, manufacture and sale of assembly and fastening materials.
Many thousands of parcels leave the dispatch centers and warehouses of Adolf Würth GmbH & Co. KG. Würth relies on SYNCROTESS from INFORM to relieve the burden on yard management and create complete transparency in the face of annually increasing transport orders and scheduling efforts.
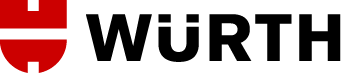
Improvement through efficiency
"We have not only managed to map the entire yard processes in such a way that the dispatchers can get an overview at a glance, but also to reduce the workload so much that, despite growth, the task can still be handled well by the existing team."
Roman Kessler, Project Manager Transport Control Center at Würth
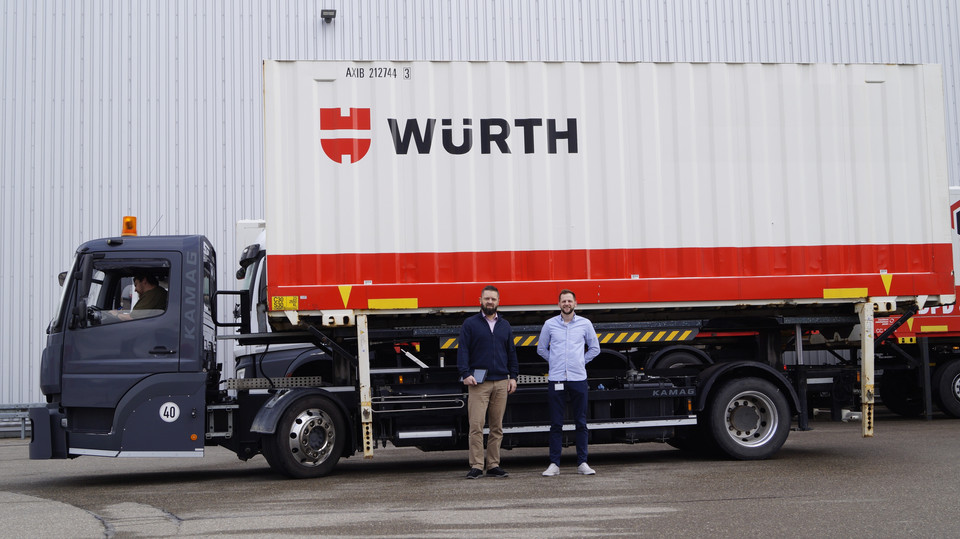
The three main distribution centers in Gaisbach and the central external warehouse in Waldenburg, which was built in 2020, are located close to the Würth headquarters in Gaisbach, Baden-Württemberg, between Stuttgart and Nuremberg. Here, in the idyllic Hohenlohe region near the Würth Group's headquarters in Künzelsau, the company dispatches its range of over 125,000 items to locations and customers all over the world. However, the swap bodies are not collected by companies such as DPD, GLS, Schenker, and Dachser from a single yard, but from several dispatch points within a radius of around 50 kilometers: the dispatch centers hold the loaded swap bodies, usually in trains of two, at various staging areas for collection.
A shunting vehicle operated by Würth has the task of moving the swap bodies, some of which are company-specific, from the gates to the staging areas after they have been loaded, as well as bringing empty swap bodies to the gates. In particular, the fixed daily, multiple departures of the individual shipping service providers must be taken into account. At the agreed time, a truck from the respective service provider arrives at the yard in question to pick up two loaded swap bodies. Delays must be limited to a maximum tolerance range of ten minutes so that the goods reach the transshipment centers on time. Since 2020, Würth has been using SYNCROTESS software from international optimization specialist INFORM to achieve complete transparency in yard management, significantly simplify scheduling, and ensure process reliability.
Robust processes despite increasing complexity
The aim of the collaboration was to achieve transparency and control over the processes in the loading yard. Where Excel, phone calls, and paper notes used to ensure management and communication between the dispatcher and the shunting vehicle, the Intralogistics Management system from the Aachen-based software manufacturer now provides user-friendly control options, an overview, and opportunities for error-free, effective dispatching. The media previously used did not provide a data basis for this.
Around 60 swap bodies and 40,000 parcels leave the yard every day. "We have not only managed to map the entire yard processes in such a way that the dispatchers can get an overview at a glance but also to reduce the workload so much that, despite growth, the task can still be handled well by one specialist per shift," confirms Roman Kessler, Project Manager Transport Control Center at Würth. Minimizing sources of error was also one of the goals of the collaboration. For example, a large part of the communication between the management and the shunting vehicle used to take place over the telephone with loud background noise. This could lead to misunderstandings when transferring and recording jumper numbers. Transmitting some information via written notes on paper after a last-minute change was also outdated and led to delays in communication. According to Kessler, digital control is also a great advantage for the introduction of new employees in terms of process reliability. After all, it is important to keep an eye on and coordinate many resources and times in a dynamic process.
Accordingly, the most important PKI was the control of departure times. The loaded swap bodies must be available for the incoming trucks on time according to the schedule agreed with the service providers. It is up to the scheduling department to decide which swap body should be assigned to which departure. All this is now controlled via SYNCROTESS.
Tailor-made user interface
In order to find a suitable solution provider, Würth invited several suppliers. The choice fell on INFORM, which impressed with its extensive options for customizing the software, among other things. For example, the specific view for Yard Management was newly developed especially for the application at Würth. The aim was to map the entire loading yard, three dispatch centers, and external warehouses with all gates, which are located at different geographical locations, on a single screen. This was to include a complete display of all loading ramps and departures.
To achieve this result, several workshops were held on site at Würth. These were not just about designing the processes. An INFORM employee had the opportunity to accompany the various end users - dispatchers, shunting vehicle drivers, loaders, gatekeepers - at work for hours in order to record all tasks and, thus, gather the necessary requirements and wishes for the user-friendliness of the new screen. "INFORM's approach led to a high level of acceptance among the
users, so that we hardly had any need for time-consuming change management," confirms Kessler. "We are still benefiting from this today." The development and implementation project ran from September 2019 to May 2020 and was accepted on time. The software has been in operation ever since.
Dynamic control and automation
Dispatchers at Würth are now able to assign swap bodies to specific departures in any order or to make them available at a gate using drag'n'drop. The drivers of the shunting vehicle then receive instructions on their tablet and can confirm completed orders there or store special information. Color coding and small symbols show the dispatchers at a glance which service provider a swap body belongs to and its current status (e.g. "planned" / "being loaded" / "loaded"). "I think it's brilliant how much information we can record in a focused way on one screen," says Kessler. "We can see all the gates and all the departures in the entire daily schedule grouped by transport service provider and then sub-grouped again by subcontractor."
"Today, we monitor the departure of every single swap body and record this information in the system. This target time control has enabled us to achieve data transparency with SYNCROTESS," adds Kessler. "The system also helps us to document other key figures." This is helpful for managing the service providers. If a truck is late, for example, this is now documented transparently and can be used in the handling of the disruption. "We know exactly which goods leave our yard when and when they arrive at which service provider and where."
The first automation components have also been integrated. For example, the provision of suitable, empty swap bodies at certain gates is already being ordered automatically if the previous one has been moved. Similarly, certain collective swap body transports can already be fully automated. Empty swap bodies are partially loaded at several positions and then driven to the staging area.
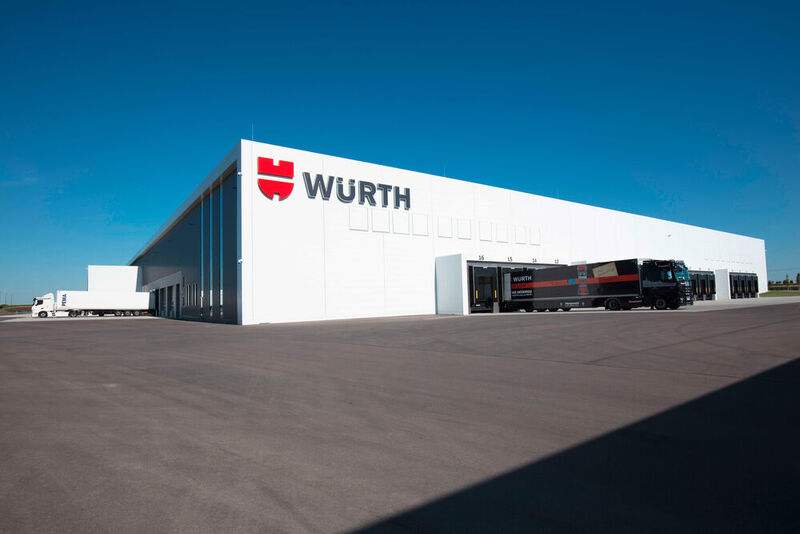
Future-proof progress
Last but not least, the project is also helping Würth on its path to a more sustainable economy. The company is committed to achieving climate neutrality by 2024 in Scope 1 and 2 according to the Greenhouse Gas Protocol, as well as circular economy capability by 2030. By using SYNCROTESS, around 60 swap bodies can be processed without additional paperwork; a contribution to Würth achieving its goals.
Operationally, preparations have also been made to include the central external warehouse in Waldenburg, where bulkier goods are currently stored and delivered, into the SYNCROTESS workflow if the use of a shunting vehicle should become necessary or practical there.
ACHIEVEMENTS
- Transparency and control over all yard processes
- Minimization of error sources thanks to automated communication
- Ensure process reliability
- Automation of the provision of suitable, empty swap bodies
- Continuous documentation