Hödlmayr Optimizes Internal Vehicle Logistics Processes with INFORM

Hödlmayr International AG, a leading vehicle logistics company, is advancing its digitalization strategy by implementing INFORM’s software solutions to manage internal logistics processes. This initiative aims to fully digitize the management of around 500,000 vehicles annually across its operations. The project begins at Hödlmayr's four Austrian locations and will gradually expand to all European sites.
Key Highlights
Comprehensive Digitalization of Logistics Processes
- Hödlmayr handles over 1.7 million vehicles annually, operating one of Europe’s largest transport fleets with 600 vehicle transporters and 20 block train systems.
- The digitalization project focuses on optimizing yard and workshop management across multiple logistics centers, enhancing efficiency and transparency.
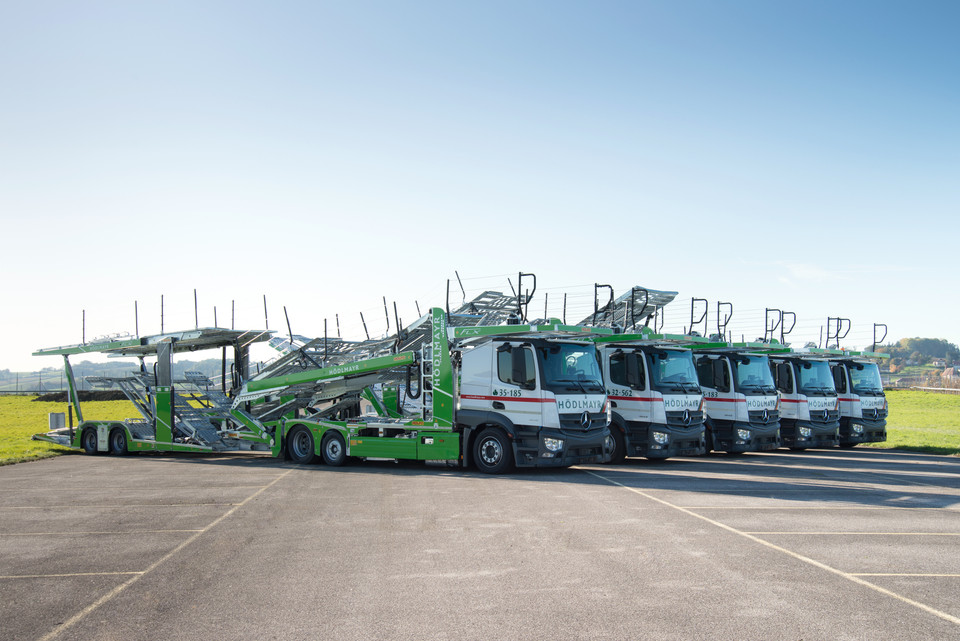
Advanced Decision Support with INFORM’s Software
- The INFORM system replaces Hödlmayr’s in-house solutions, using mathematical optimization and artificial intelligence to manage vehicle movements, parking, and workshop processes.
- The centralized control station enables real-time decision-making, optimizing task allocation and order processing based on predefined rules for each location.
Flexibility and Scalability Across Locations
- The uniform yet adaptable IT solution supports Hödlmayr in responding quickly to new processes and customer requirements, ensuring operational flexibility.
- The system’s design allows for region-specific customization while maintaining a standard approach, making it scalable across Hödlmayr’s European network.
It was important to us that we create a uniform, flexible IT solution for all yards of the Hödlmayr Group. The standard solution from INFORM supports us in this. This allows us to react independently, flexibly and as quickly as possible to new process and customer requirements.
Reducing Manual Interventions and Increasing Transparency
- The software minimizes manual interventions by providing holistic transparency over vehicle and order status, allowing dispatchers to focus only on exceptions.
- Data from all relevant sources are integrated into the system, eliminating media disruptions and enhancing overall operational coherence.
Strategic Expansion Across Europe
- Starting in Austria, the digitalization initiative will expand to Hödlmayr’s other European locations over the next four years, aiming to standardize logistics processes across the company.
- The long-term goal is to unify all logistics centers under a single, efficient IT framework, supporting Hödlmayr’s growth and adaptation to market demands.
Benefits
- Increased Efficiency:
Real-time optimization of logistics processes reduces delays and improves resource utilization. - Enhanced Transparency:
Full visibility of vehicle and order status enables better management and decision-making.
- Scalable Solution: The adaptable IT framework supports consistent service quality across multiple locations.
- Reduced Costs: Automation of logistics processes lowers operational costs and minimizes the need for manual oversight.
Conclusion
Hödlmayr International AG’s partnership with INFORM is set to transform its internal vehicle logistics, ensuring high efficiency, flexibility, and scalability across its operations. The strategic implementation of INFORM’s software solutions will enhance Hödlmayr’s ability to meet customer demands and stay competitive in the rapidly evolving logistics market.
more information
Are you interested in more information or would you like to learn how our solutions can benefit your company? Simply fill out the contact form below, and we’ll get in touch with you shortly. We look forward to hearing from you!