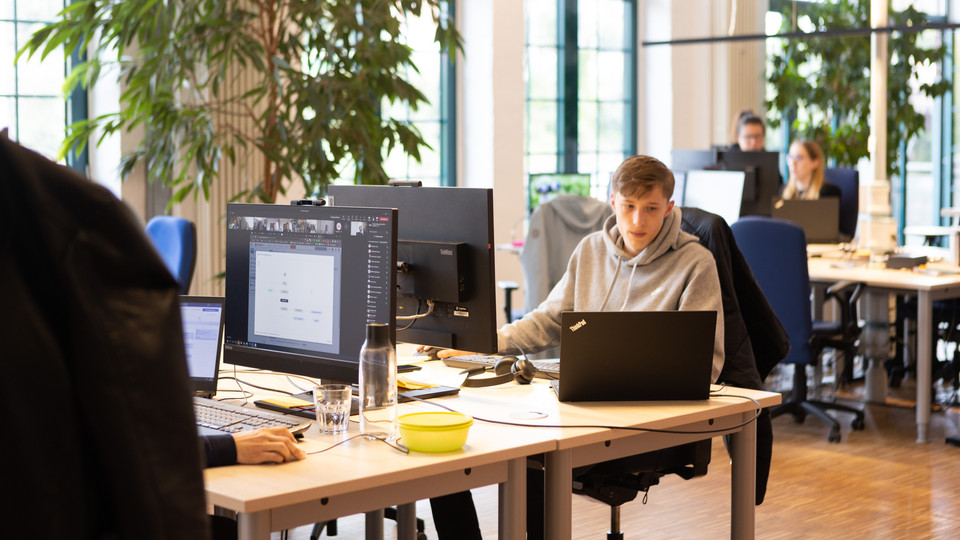
Oct 22-24, 2025 | Berlin
BVL Supply Chain CX 2025
Meet us at the BVL Supply Chain CX and experience our exclusive specialist presentation - innovative insights and practical solutions for the future of supply chain management await you!
Gain Not Only Visibility but also Foresight over Your Inventory Management
Seasonality, shorter product life cycles, constantly changing market trends, and best-before dates are all very important aspects. As an inventory manager, you face numerous challenges. Although you manage to keep track of the complex processes in inventory management, there is often a lack of transparency – the tasks in procurement planning are now too complex.
The decision-intelligent ADD*ONE solution suite helps you get a grip on this complexity. The optimization software supports you in resolving the conflicting goals between maximum delivery capability on the one hand and optimum inventories on the other, reducing costs and sustainably increasing your customers' satisfaction.
Maximum Delivery Capability, Optimum Inventories, and Complete Transparency
As add-on software, the ADD*ONE solution suite overcomes the classic limitations of your ERP system. The software supports you with AI-supported, powerful forecasts and algorithms to manage, control, and sustainably improve the supply chain in your company. With ADD*ONE, you regain full transparency over your inventories' overall situation and scheduling tasks.
Intuitive Operability and Effective Work Facilitation
ADD*ONE is intuitive to use. The planning software makes your daily work much easier by suggesting directly and conveniently which articles you should order when and in which quantity from which supplier. In doing so, ADD*ONE automatically takes into account all framework parameters from minimum order quantities to discount structures, ordering costs, packaging units to the desired service level, and much more.
More Planning Reliability
"Unwelcome surprises" are avoided by using ADD*ONE, as the software reliably alerts you to exceptions and problem cases so that you can always intervene and take countermeasures in good time.
The inventory manager fulfills the role of an all-rounder who has to consider all eventualities in operations and logistics – ADD*ONE is the basis on which this process becomes possible.
Christoph Wiericks
Expert for Supply Chain Optimization
Christoph Wiericks has been strengthening the Inventory & Supply Chain division at INFORM GmbH since 2016. With in-depth expertise in supply chain optimisation, he supports companies in selecting the right AI solutions. His particular focus is on analysing and optimising inventories and implementing efficient planning strategies. As an experienced sales specialist, he guides companies through the decision-making process and finds tailored solutions to their challenges.