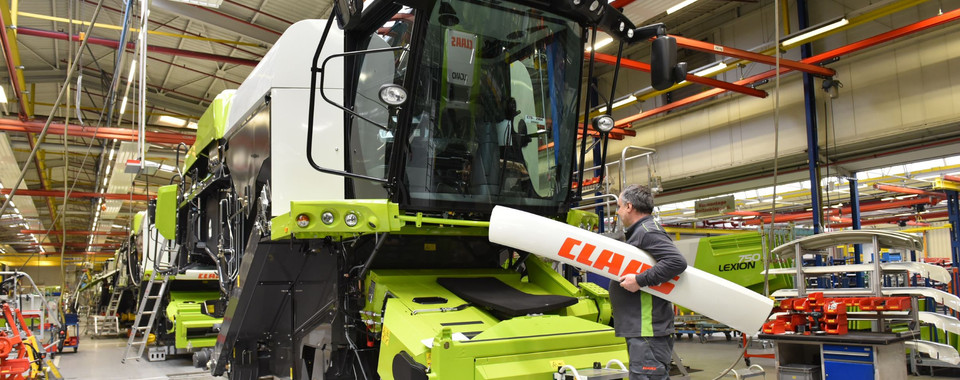
Optimized production logistics at CLAAS
The SYNCROTESS intralogistics management system controls the internal flow of materials and secures production logistics at CLAAS, the agricultural machinery manufacturer.
What does an intralogistics management system do? The specialized software supports logisticians in mastering the diverse and dynamic requirements of in-house logistics.
The complexity of modern production environments demands powerful management systems that not only manage different order types, logistics processes, vehicle, or load types, but also make optimal use of them. Thanks to the scalability and modular structure, the intralogisitcs management system can meet the growing production logistics requirements of companies of various sizes.
How does the intralogistics management software SYNCROTESS work?
What features are covered and what benefits does SYNCROTESS offer?
Our brochure answers these and other questions.
For in-house logistics, complex production processes mean the increasing variety of individual parts must be made available for production on time. Material flow processes have to be optimally coordinated in order to supply production with the right material in the right quantity and quality at the right time and in a cost-effective manner.
Our intralogistics management system synchronizes production and logistics processes. Real-time scheduling enables transparent transport control, where planners can react quickly and appropriately to unforeseen events.
The implementation of a complete logistics concept with a intralogistics management system results in:
The agricultural machinery manufacturer CLAAS Selbstfahrende Erntemaschinen GmbH uses the intralogistics management system SYNCROTESS from INFORM to cope with the growing complexity of the internal material flow for combine harvesters, forage harvesters and the like.